Specific Requirements of Digital Avionics for Cables
Modern aircraft rely heavily on digital avionics systems to ensure safety, efficiency, and performance. At the heart of these systems are specialized cables designed to meet the rigorous demands of aviation environments. Understanding the specific requirements of digital avionics for cables is critical for engineers, technicians, and aviation stakeholders. This article explores the essential criteria for avionics cables, offering actionable insights to address real-world challenges.
1. EMI/RFI Shielding: Protecting Signal Integrity
Digital avionics systems operate in environments saturated with electromagnetic interference (EMI) and radio frequency interference (RFI). Cables must incorporate multi-layered shielding (e.g., braided copper, foil, or composite materials) to prevent signal degradation.
- Best Practice: Use cables with MIL-STD-461 or DO-160 compliance to ensure EMI/RFI resistance.
- Failure Risk: Unshielded cables can disrupt critical systems like flight controls or navigation.
2. Temperature and Environmental Durability
Avionics cables face extreme temperatures (-55°C to 200°C), moisture, and chemical exposure.
- Material Selection: Opt for PTFE (Teflon) or ETFE insulation for high thermal stability.
- Certification: Ensure compliance with FAA or EASA standards for fire resistance (e.g., FAR 25.853).
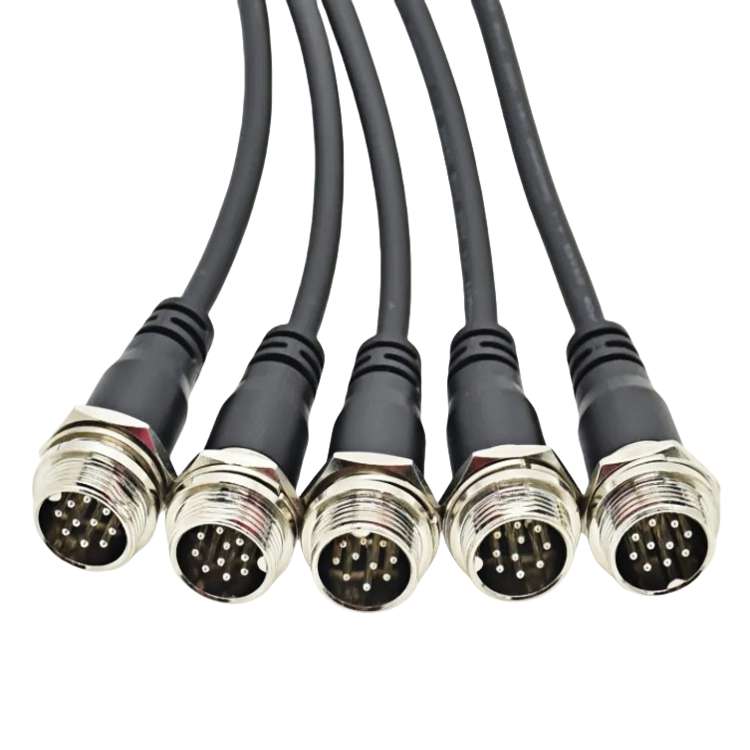
3. Mechanical Strength and Flexibility
Aircraft vibrations, flexing, and repeated maintenance require cables to balance durability and flexibility.
- Design Tip: Use stranded conductors instead of solid-core wires to withstand vibration fatigue.
- Testing: Perform bend cycle tests (e.g., MIL-W-22759) to validate longevity.
4. Weight and Space Optimization
Aerospace design prioritizes weight reduction. Lightweight cables with high conductor efficiency (e.g., aluminum or copper-clad aluminum) reduce fuel consumption.
- Innovation: Fiber-optic cables offer high-speed data transmission with minimal weight.
5. Fire Safety and Smoke Toxicity
Avionics cables must meet strict flammability standards to prevent fire hazards.
- Key Standards: AS/EN 3475-501 for low smoke/toxicity, FAR 25.853 for flame resistance.
- Material Choice: Silicone or fluoropolymer jackets resist ignition and limit toxic fumes.
6. Signal Integrity and Bandwidth
High-speed data buses (e.g., ARINC 429, AFDX) demand cables with controlled impedance and minimal crosstalk.
- Solution: Twisted-pair or coaxial designs with precise dielectric properties.
- Testing: Use time-domain reflectometry (TDR) to verify signal performance.
7. Connector Compatibility
Avionics cables require ruggedized connectors (e.g., MIL-DTL-38999) to maintain reliability in harsh conditions.
- Pro Tip: Opt for gold-plated contacts to prevent corrosion and ensure conductivity.
8. Compliance with Industry Standards
Avionics cables must align with aviation-specific regulations:
- MIL-STD-704: Electrical power characteristics.
- DO-160: Environmental testing for airborne equipment.
- SAE AS22759: Wire and cable performance criteria.
9. Maintenance and Inspection Protocols
Regular cable inspections are vital for safety.
- Checklist: Look for abrasions, cracked insulation, or corrosion.
- Tools: Use continuity testers and megohmmeters to detect hidden faults.