Aviation Cable Welding Technology
In the aerospace industry, where safety and reliability are paramount, welding aviation cables is not just a technical process—it’s a discipline governed by rigorous international standards. These standards ensure that every welded joint in an aircraft’s electrical system can withstand extreme conditions, from supersonic vibrations to cryogenic temperatures. As aircraft become more globally integrated, harmonizing welding practices across borders has become critical.
- Key Standard-Setting Organizations
Aviation cable welding standards are developed by a network of global organizations:
ISO (International Organization for Standardization): Provides foundational guidelines, such as ISO 4063 (welding process classification) and ISO 14327 (resistance welding qualifications).
SAE International: Publishes AS6081, focusing on counterfeit avoidance in electrical components, and AMS 2680 for aerospace resistance welding.
IEC (International Electrotechnical Commission): Standards like IEC 62137 address reliability of soldered joints in avionics.
NADCAP (National Aerospace and Defense Contractors Accreditation Program): Certifies welding processes through audits aligned with AS9100 quality management systems.
2. Welding Process Standards
A. Material Compatibility
Standards mandate precise control over base metals and filler materials:
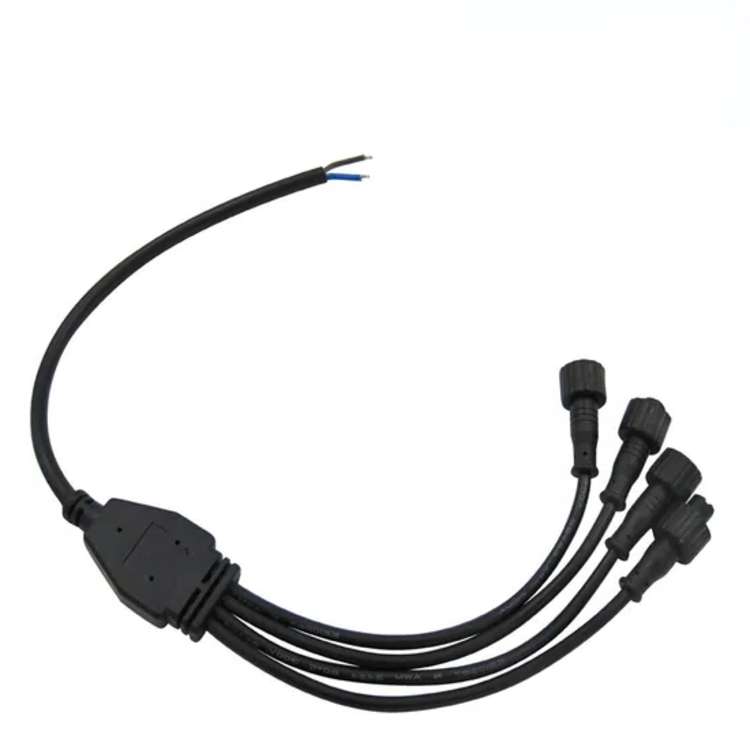
ISO 14327: Specifies weldability testing for dissimilar metals (e.g., copper to aluminum joints).
SAE AMS 2680B: Requires tensile strength ≥90% of base metal for resistance-welded nickel alloys.
B. Process Parameters
Laser Welding: Per ISO 15614-11, laser power must stay within ±2% of specified levels to avoid HAZ (heat-affected zone) defects.
Ultrasonic Welding: MIL-STD-1941 defines amplitude (10–50 µm) and pressure (0.2–1.5 MPa) ranges for aerospace-grade bonds.
C. Joint Design
IEC 62137-2: Requires fillet welds in avionics connectors to have a minimum throat thickness of 0.8× conductor diameter.
NASA-STD-5002: Prohibits lap joints in high-voltage cables (>270V) due to arcing risks.
3. Inspection and Testing Protocols
A. Non-Destructive Testing (NDT)
ISO 17635: Mandates radiographic or ultrasonic inspection for critical welds in engine and flight control systems.
Penetrant Testing: Per ASTM E1417, used to detect surface cracks in aluminum welds.
B. Destructive Testing
ISO 4136: Tensile tests must confirm weld strength meets or exceeds 95% of base material.
Metallographic Analysis: ASTM E3 requires cross-sectional examination to verify absence of voids or inclusions.
C. Environmental Simulation
Welds undergo aging tests per RTCA DO-160:
Thermal Cycling: -55°C to 125°C for 500 cycles.
Salt Spray: 48-hour exposure to 5% NaCl solution.
4. Certification and Compliance Challenges
A. NADCAP Accreditation
Suppliers must pass audits covering:
Welder Qualifications: Documentation of training per AWS D17.1 (Aerospace Welding Standard).
Traceability: All materials must comply with AS5553 counterfeit prevention measures.
Case Study: In 2022, a Tier-2 supplier for Airbus A220 faced NADCAP suspension after failing to maintain weld parameter logs for titanium coaxial cables.
B. Regional Variations
FAA (U.S.): Adheres to AC 43.13-1B for repair welding, requiring 100% visual inspection.
EASA (Europe): Under Part 21G, welding procedures must be validated via EN 15085 for large aircraft.
C. Cost and Complexity
Achieving compliance often requires:
Advanced Equipment: Laser welding systems meeting ISO 11553 safety protocols cost
500
–
500K–1M.
Staff Training: Welding engineers must complete EWF/IIW certifications for international projects.
5. Emerging Trends in Standardization
Digital Compliance: Blockchain-based traceability systems (e.g., Siemens’ Teamcenter) automate AS9100D documentation.
Additive Welding Standards: Draft guidelines for 3D-printed conductive joints (ISO/ASTM 52900).
Green Welding: ISO 14064 pushes for reduced GHG emissions in welding processes.