Aircraft Cable Alternatives: Optimal Use Cases for Fiber Optic and A...
Modern aviation demands lightweight, efficient, and reliable wiring solutions. While traditional copper cables have long dominated aircraft systems, fiber optic and aluminum cables are emerging as viable alternatives for specific applications.
Why Consider Alternatives to Copper Cables?
Copper cables, though reliable, face growing scrutiny due to:
Weight: Copper’s density increases fuel consumption.
EMI susceptibility: Vulnerable to electromagnetic interference in densely packed avionics.
Cost: Rising copper prices strain budgets.
Fiber optic and aluminum cables address these issues while excelling in niche roles.
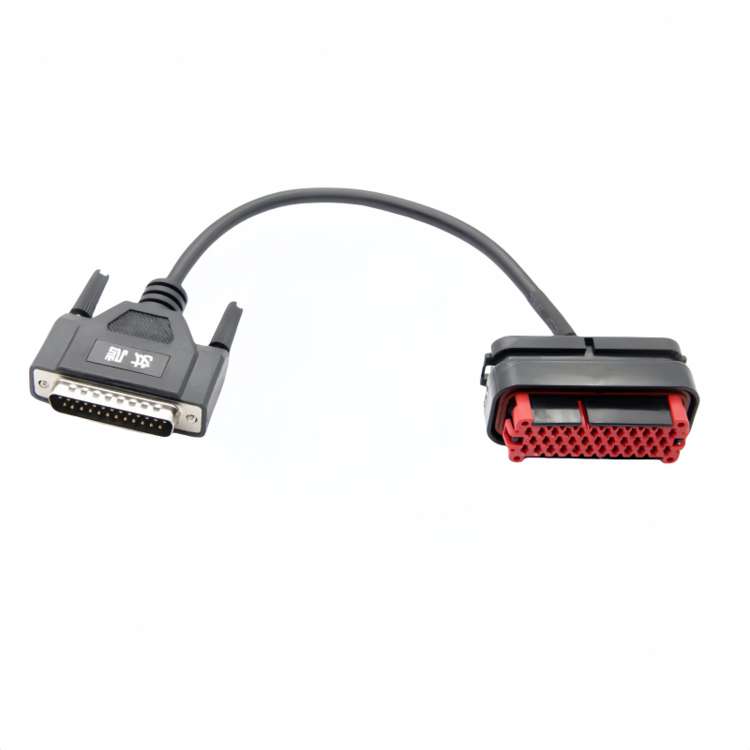
Fiber Optic Cables: High-Speed Data in Harsh Environments
Key Advantages
Ultra-Lightweight: 70% lighter than copper, reducing aircraft weight and fuel costs.
EMI Immunity: Immune to electromagnetic interference, ideal for critical avionics.
Bandwidth: Supports gigabit+ speeds for real-time data (e.g., fly-by-wire, in-flight entertainment).
Durability: Resists corrosion, extreme temperatures (-65°C to +200°C), and vibration.
Challenges
Fragility: Requires careful handling during installation.
Cost: Higher upfront investment than copper or aluminum.
Power Limitations: Cannot transmit electrical power.
Ideal Use Cases
Avionics Networks:
ARINC 664 (AFDX) for flight control data.
High-definition cockpit displays and sensors.
In-Flight Entertainment (IFE):
Streaming 4K video to passenger screens.
Military Systems:
Secure, jam-resistant communication links (MIL-STD-883 compliant).
Standards: ARINC 801, MIL-DTL-83526.
Aluminum Cables: Cost-Effective Power Distribution
Key Advantages
Weight Savings: 50% lighter than copper, improving fuel efficiency.
Cost-Efficiency: Aluminum is 60–70% cheaper than copper.
Corrosion Resistance: Anodized coatings protect against moisture and chemicals.
Challenges
Lower Conductivity: Requires thicker gauges to match copper’s current capacity.
Thermal Expansion: Prone to loosening at connections if not properly secured.
Fatigue Resistance: Less durable under repeated bending.
Ideal Use Cases
Non-Critical Power Systems:
Cabin lighting, galley equipment, and auxiliary power units (APUs).
Ground Support Infrastructure:
Hangar power grids and charging stations for electric aircraft.
Short-Run Wiring:
Non-load-bearing applications like seat actuators or HVAC controls.
Standards: SAE AS50881, MIL-W-5088.
Fiber Optic vs. Aluminum: How to Choose?
Factor Fiber Optic Aluminum
Primary Purpose High-speed data, EMI-sensitive systems Cost-sensitive power distribution
Weight Best for weight-critical designs Lighter than copper, heavier than fiber
Durability Excellent in harsh environments Requires corrosion-resistant coatings
Installation Cost High (specialized tools/skills) Low (similar to copper)
Implementation Best Practices
Hybrid Systems:
Combine fiber optics for data and aluminum for power (e.g., Boeing 787 Dreamliner’s fiber-based avionics).
Connector Optimization:
Use MIL-DTL-38999 connectors for fiber optics to prevent signal loss.
Apply antioxidant pastes on aluminum terminals to reduce corrosion.
Testing:
Conduct TDR (Time-Domain Reflectometry) tests for fiber optic integrity.
Perform thermal cycling tests on aluminum joints.
Future Trends
Smart Cables: Fiber optics with embedded sensors for real-time health monitoring.
Composite Aluminum Alloys: Improved conductivity and fatigue resistance.
5G Integration: Fiber optics enabling onboard 5G networks for connected aircraft.