Which Types of Cables Are Suitable for Avionics
Avionics systems are the backbone of modern aircraft, ensuring navigation, communication, and operational safety. Choosing the right cables for these systems is critical to maintaining reliability, compliance, and performance in demanding aerospace environments. In this guide, we’ll explore the best cable types for avionics, their key features, and how to select the right ones for your needs.
Key Considerations for Avionics Cables
Avionics cables must meet stringent standards to withstand extreme conditions while ensuring signal integrity and safety. Here’s what to prioritize:
- Temperature Resistance: Cables must endure wide temperature ranges (-55°C to 200°C+).
- Flexibility and Durability: Vibration, bending, and mechanical stress are common in aircraft.
- EMI/RFI Shielding: Protection against electromagnetic and radio frequency interference is non-negotiable.
- Weight and Size: Lightweight, compact designs reduce fuel consumption and save space.
- Regulatory Compliance: Adherence to MIL-SPEC, SAE AS, or DO-160 standards is mandatory.
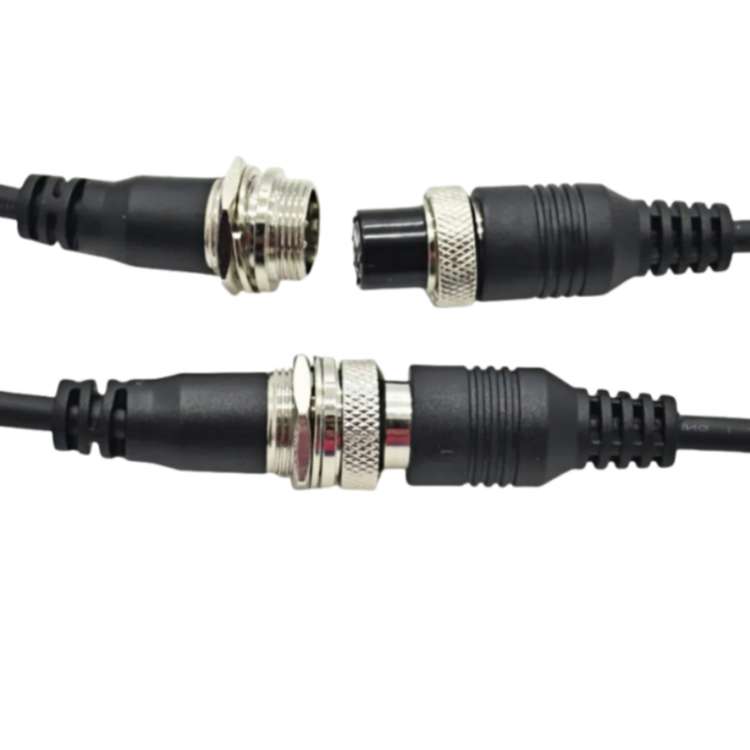
Top Cable Types for Avionics Systems
1. Coaxial Cables
- Use Case: Transmitting high-frequency signals (e.g., radar, GPS, communication systems).
- Key Features:
- Dual shielding (braided + foil) for superior EMI protection.
- PTFE (Teflon) insulation for heat resistance.
- Compliant with MIL-DTL-17 standards.
- Common Variants: RG-142, RG-400.
2. Twisted Pair Cables
- Use Case: Data transmission (e.g., avionics buses, Ethernet networks).
- Key Features:
- Twisted conductors reduce crosstalk and noise.
- Often shielded (STP) for EMI protection.
- MIL-DTL-27500 or SAE AS22759 compliant.
3. Shielded Multi-Conductor Cables
- Use Case: Power distribution and low-voltage signal transmission.
- Key Features:
- Multiple insulated conductors bundled under a single shield.
- High-temperature insulation like PTFE or FEP.
- MIL-DTL-81381 or MIL-DTL-915 compliant.
4. Fiber Optic Cables
- Use Case: High-speed data transfer (e.g., in-flight entertainment, flight control systems).
- Key Features:
- Immune to EMI and lightning strikes.
- Lightweight with high bandwidth.
- Compliant with MIL-STD-2042 or ARINC 801 standards.
5. High-Temperature Hook-Up Wire
- Use Case: Internal wiring for avionics equipment.
- Key Features:
- Silicone or PTFE insulation for extreme heat resistance.
- Thin walls to save space.
- MIL-W-22759/16 or SAE AS22759/32 compliant.
6. Thermocouple Extension Cables
- Use Case: Temperature sensors in engines or environmental systems.
- Key Features:
- Alloy-matched conductors (e.g., Type K, J) for accurate readings.
- High-temperature jackets (e.g., fiberglass).
How to Choose the Right Avionics Cable
- Verify Compliance: Ensure cables meet MIL-SPEC, SAE AS, or RTCA DO-160 standards.
- Assess Environmental Factors: Consider exposure to heat, moisture, chemicals, and abrasion.
- Prioritize Shielding: Opt for double-shielded or triple-shielded designs in high-EMI zones.
- Consult Manufacturers: Work with aerospace-certified suppliers like CarlisleIT, TE Connectivity, or Amphenol.
- Test Extensively: Validate performance under simulated operational conditions.
Best Practices for Avionics Cable Maintenance
- Regular Inspections: Check for fraying, corrosion, or damaged shielding.
- Proper Routing: Use clamps and conduits to avoid chafing against sharp edges.
- Labeling: Clearly mark cables for easy troubleshooting.
- Follow OEM Guidelines: Adhere to aircraft manufacturer recommendations for replacements.
Why Material Matters in Avionics Cables
- PTFE (Teflon): Excellent for high temps and chemical resistance.
- ETFE: Lightweight with good flexibility.
- Silicone: Extreme temperature tolerance (-90°C to 200°C).
- Fiberglass: Ideal for fire-resistant applications.