Advances in Early Warning Systems for Aviation Cable Failures
In the aerospace industry, where system failures can have catastrophic consequences, the reliability of aviation cables is non-negotiable. These cables, responsible for transmitting power, data, and control signals, are subjected to extreme operational stresses—from thermal cycling and vibration to chemical corrosion. Traditional reactive maintenance approaches, which address failures after they occur, are increasingly inadequate for modern aircraft. Enter early warning systems (EWS): technologies designed to predict and prevent cable failures before they disrupt operations.
1. The Critical Role of Welding in Aviation Cables
Aviation cables operate in environments characterized by vibration, thermal cycling, and electromagnetic interference. A single faulty connection can disrupt flight systems, making welding quality paramount. Key applications include:
Power Distribution: Welded joints in high-voltage cables for engines and actuators.
Signal Transmission: Precision connections in fiber-optic and coaxial cables for avionics.
Sensor Networks: Micro-welds in strain gauges and temperature sensors embedded in wings or landing gear.
Traditional soldering and resistance welding often fall short due to brittleness, heat-affected zones (HAZ), and inconsistent results in miniaturized components.
2. Challenges in Aviation Cable Welding
A. Material Compatibility
Modern aircraft use diverse materials, from copper and aluminum to advanced alloys and composites. Each requires tailored welding approaches:
Dissimilar Metals: Joining aluminum conductors to copper terminals without intermetallic brittleness.
High-Temperature Alloys: Welding nickel-based superalloys in engine bay cables demands precise heat control.
B. Miniaturization
As avionics shrink, cable diameters and connector sizes follow suit. For example:
Micro-D connectors with 0.05mm pins require sub-micron welding accuracy.
Fiber-optic splices demand alignment tolerances under 1µm to prevent signal loss.
C. Durability Under Stress
Welds must withstand:
Thermal Cycling: -55°C to 200°C fluctuations in supersonic aircraft.
Vibration: Up to 20G forces in military jets.
Corrosion: Exposure to de-icing fluids and salt-laden atmospheres.
3. Technological Breakthroughs in Welding Processes
A. Laser Welding
Pulsed and continuous-wave lasers enable pinpoint accuracy with minimal HAZ:
Fiber Laser Welding: Used for copper-aluminum joints in Boeing’s 787 Dreamliner, achieving 99% conductivity efficiency.
Green Lasers (515nm): Optimized for highly reflective materials like gold-plated connectors in satellite systems.
Case Study: Airbus’s A350 employs laser-welded titanium coaxial cables, reducing weight by 15% compared to soldered counterparts.
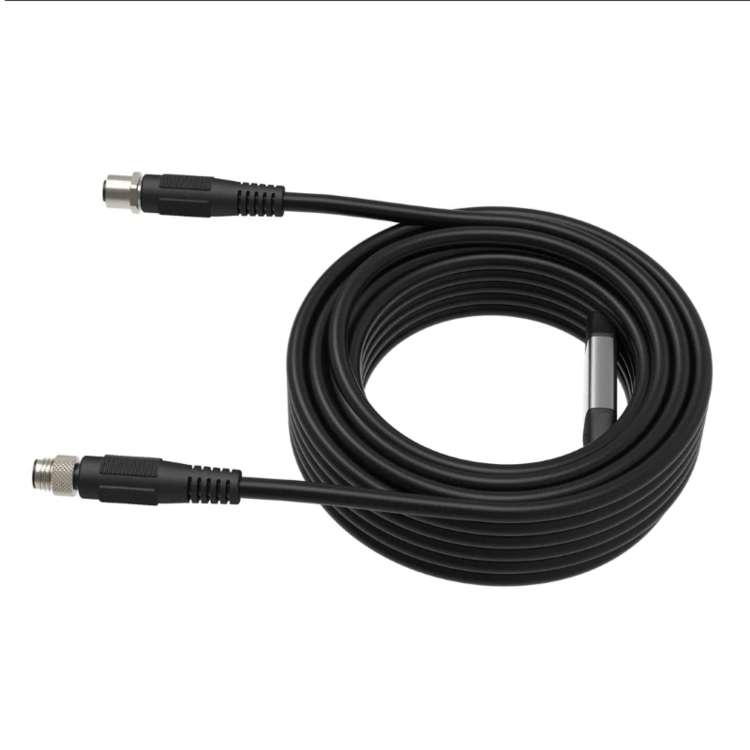
B. Ultrasonic Welding
This solid-state process bonds materials through high-frequency vibrations, ideal for delicate or heat-sensitive components:
Fiber-Optic Alignment: Ultrasonic welding secures silica fibers without thermal distortion, critical for in-flight entertainment systems.
Battery Connections: Used in electric aircraft (e.g., Eviation Alice) to weld lithium-ion cell terminals with zero porosity.
C. Micro-TIG Welding
Micro Tungsten Inert Gas (TIG) welding combines precision arc control with inert gas shielding:
Aerospace Sensors: Welds 0.2mm thermocouples in Pratt & Whitney’s Geared Turbofan engines.
Hermetic Seals: Creates leak-proof joints for avionics boxes exposed to high-altitude pressures.
D. Additive Welding
3D-printed conductive traces and connectors are gaining traction:
Nano Silver Inks: Jetted onto polymer substrates to form flexible circuits, welded via laser sintering.
Hybrid Harnesses: GE Additive’s Concept Laser machines print and weld custom cable brackets for Airbus A220 cabin systems.
4. AI and Automation: Elevating Quality and Speed
To meet aviation’s zero-defect standards, welding systems now integrate:
Machine Vision: Cameras inspect welds in real-time, detecting cracks or misalignments at 1000 fps.
Adaptive Control Algorithms: Adjust laser power or arc voltage dynamically based on material feedback.
Digital Twins: Simulate welding processes for new materials, reducing trial-and-error in R&D.
Example: Safran’s Smart Welder uses AI to optimize parameters for each cable batch, cutting defect rates by 40% in helicopter wiring.
5. Certification and Cost Barriers
Despite their advantages, advanced welding technologies face hurdles:
Stringent Standards: Compliance with AS9100 and NADCAP mandates extensive documentation and testing.
High Capital Costs: Laser welding setups can exceed $500,000, limiting adoption among smaller suppliers.
Skill Gaps: Operators require training in both metallurgy and software management.
6. Future Trends
Quantum Welding: Using electron beams at cryogenic temperatures for superconducting cable joints.
Self-Monitoring Welds: Embedding microsensors into joints to track degradation in real-time.
Green Welding: Hydrogen-based shielding gases and low-energy processes to align with aviation’s net-zero goals.