From Boeing to Airbus: The Current State of the Global Aerospace Wiri...
The aerospace industry’s reliance on intricate wiring systems—often described as the “nervous system” of modern aircraft—has never been more critical. Wiring harnesses, which transmit power, data, and signals across an aircraft, are essential to the functionality of everything from commercial airliners to military jets. As demand for new aircraft surges post-pandemic, the supply chains feeding giants like Boeing and Airbus face unprecedented challenges and transformations.
1. The Backbone of Modern Aviation
A single commercial aircraft contains hundreds of kilometers of wiring, with complex harnesses integrating thousands of connectors, sensors, and cables. These systems are vital for avionics, in-flight entertainment, engine controls, and safety mechanisms. Both Boeing and Airbus depend on a sprawling global network of suppliers to deliver these components, which must meet rigorous safety and performance standards.
Key players in this niche market include established aerospace suppliers like Safran (France), TE Connectivity (Switzerland), Amphenol (US), and Collins Aerospace (US), as well as specialized manufacturers such as GKN Aerospace and Labinal (now part of Safran). Emerging economies, particularly Mexico, India, and Morocco, have also become hubs for low-cost, high-precision wiring harness production.
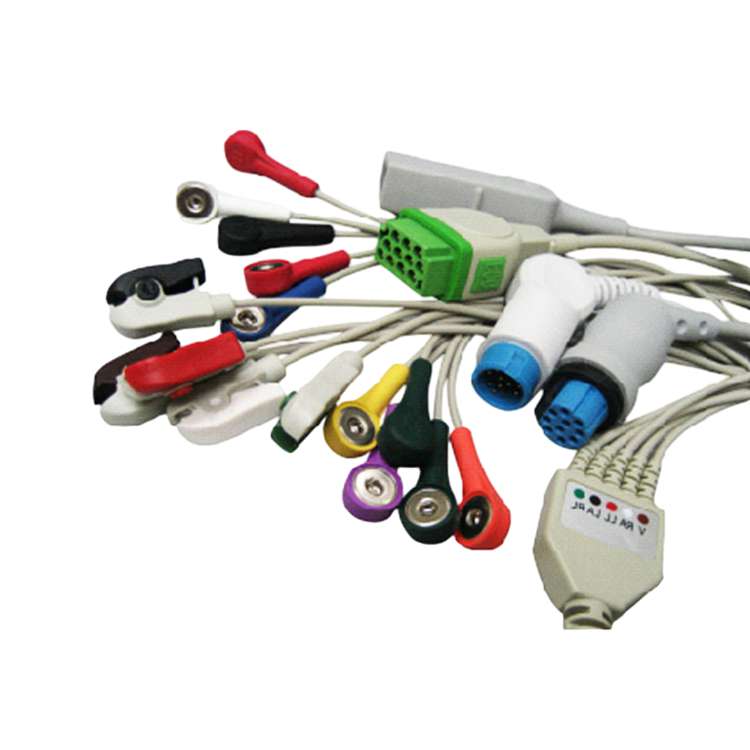
2. Supply Chain Pressures and Disruptions
The aerospace wiring supply chain has been strained by multiple factors:
Post-Pandemic Demand Surge: Airlines are rushing to modernize fleets and meet pent-up travel demand, pushing Boeing and Airbus to ramp up production. Airbus aims to deliver 800 aircraft annually by 2025, while Boeing targets 50+ 737 MAX jets per month. This urgency cascades down to wiring harness suppliers, who must scale operations without compromising quality.
Geopolitical Tensions: Sanctions, trade wars, and regional instability have disrupted material flows. For instance, the Russia-Ukraine conflict has impacted the supply of specialty metals used in connectors, while U.S.-China trade restrictions complicate sourcing for avionics components.
Labor and Material Shortages: The industry faces a scarcity of skilled technicians for precision wiring assembly. Additionally, shortages of copper, aluminum, and high-performance insulation materials (e.g., Teflon) have led to price volatility and delays.
Boeing’s Ongoing Challenges: The 737 MAX crisis and recent quality control scandals have forced Boeing to reassess its supply chain dependencies. For wiring harnesses, this has meant diversifying suppliers and increasing oversight of tier-2 and tier-3 partners.
3. Airbus vs. Boeing: Diverging Strategies
Airbus and Boeing are adopting contrasting approaches to mitigate risks:
Airbus’s Vertical Integration: Airbus has invested in vertical integration, acquiring wiring harness specialists like Labinal to secure control over critical processes. Its “Wiring Integration Center” in Bremen, Germany, centralizes harness design and testing, reducing reliance on external suppliers.
Boeing’s Supplier Diversification: After setbacks tied to single-source dependencies, Boeing has expanded its supplier base. For example, it now sources wiring systems for the 787 Dreamliner from multiple global partners, including Japan’s Yazaki and Mexico’s Cable Technologies.
Both companies are also pushing suppliers to adopt digital tools like AI-driven quality assurance and blockchain for traceability, aiming to enhance transparency across tiers.
4. The Rise of Regionalization
To counter geopolitical and logistical risks, aerospace OEMs are increasingly favoring regional supply chains. Airbus, for instance, has expanded wiring harness production in Tunisia and Mexico to serve its final assembly lines in Toulouse and Mobile, Alabama. Similarly, Boeing’s partnerships in Southeast Asia and India aim to balance cost efficiency with redundancy.
However, regionalization faces hurdles. Strict aerospace certifications (e.g., AS9100) limit the pool of qualified suppliers, while higher labor costs in nearshore locations like Eastern Europe challenge the industry’s cost-saving models.
5. Sustainability and Innovation
Environmental regulations are reshaping the wiring harness ecosystem. The EU’s SCIP database and REACH restrictions mandate stricter reporting on hazardous substances, pushing suppliers to adopt eco-friendly materials like halogen-free insulation. Meanwhile, lightweight composite cables and additive manufacturing are emerging as solutions to reduce aircraft weight and carbon emissions.
6. Looking Ahead: Resilience Through Collaboration
The aerospace wiring harness supply chain is at a crossroads. While Boeing and Airbus drive innovation through next-gen programs like the 777X and A321XLR, suppliers must navigate a maze of technical, economic, and political challenges. Success will hinge on collaboration—shared data platforms, joint R&D investments, and flexible production models—to build a supply chain resilient enough to weather future shocks.