Electromagnetic Shielding Technology in Aviation Cables
Introduction
In the complex electromagnetic environment of modern aircraft, reliable communication and data transmission are non-negotiable. Aviation cables, which connect critical systems like avionics, radar, and flight controls, face relentless exposure to electromagnetic interference (EMI) from engines, onboard electronics, and external sources such as lightning or radio waves. Ensuring “zero-interference” communication demands advanced electromagnetic shielding technologies.
1.The Threat of EMI in Aviation
Electromagnetic interference poses significant risks to aircraft safety and performance:
Signal Degradation: EMI can corrupt data transmitted between systems, leading to errors in navigation, engine control, or flight instrumentation.
Safety Hazards: Unshielded cables near high-power systems (e.g., radar or electric propulsion) risk triggering short circuits or false alarms.
Regulatory Compliance: Standards like RTCA DO-160 and MIL-STD-461 mandate rigorous EMI testing for aviation components.
For example, during a 2019 incident, EMI from a passenger’s electronic device temporarily disrupted a Boeing 737’s communication system, underscoring the need for robust shielding.
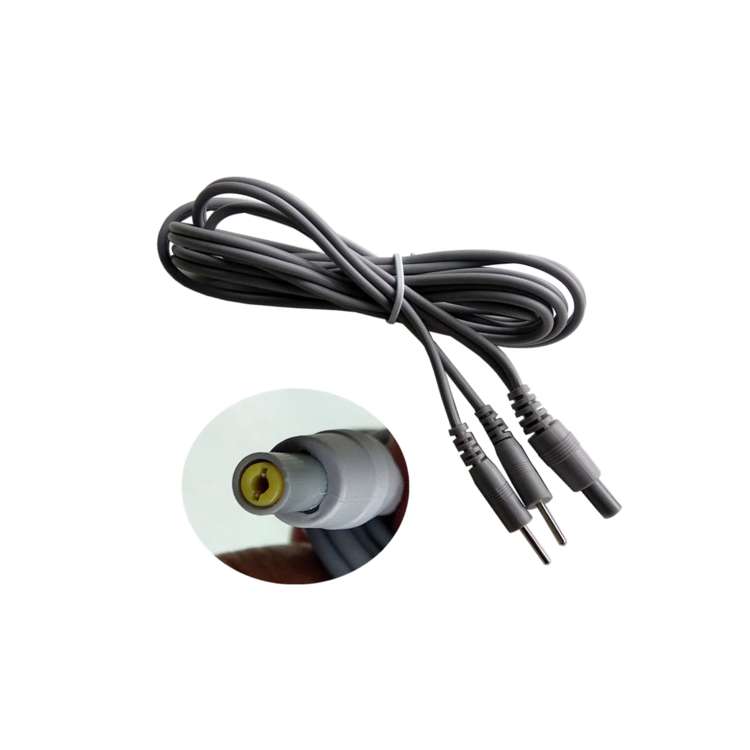
2. Core Principles of Aviation Cable Shielding
Shielding techniques aim to block or redirect electromagnetic waves away from sensitive conductors. Key methods include:
a. Conductive Shielding Layers
Braided Shields: Interwoven metal strands (often copper or aluminum) form a flexible, high-coverage barrier around cables.
Advantage: Provides 85–95% EMI protection and mechanical durability.
Use Case: Widely used in fly-by-wire systems for military aircraft like the F-22 Raptor.
Foil Shields: Thin aluminum or copper foil wraps offer lightweight, full-coverage shielding.
Advantage: Ideal for high-frequency interference in commercial aircraft communication cables.
b. Multi-Layered Shielding Architectures
Combining braided and foil shields creates redundant protection:
Example: Airbus A380’s engine control cables use a triple-layer design (foil + braid + drain wire) to suppress EMI from high-thrust engines.
c. Conductive Polymers and Nanomaterials
Carbon-Nanotube (CNT) Coatings: Lightweight, flexible materials that absorb and dissipate EMI.
Conductive Plastics: Polymers infused with metallic particles provide shielding while reducing cable weight.
3. Advanced Shielding Technologies in Action
a. Frequency-Selective Shielding
Technology: Shields tailored to block specific EMI frequencies (e.g., 2.4 GHz from Wi-Fi or 5G networks).
Application: Protects in-flight entertainment systems in Boeing 787 Dreamliners from passenger device interference.
b. Hybrid Optical-Electrical Cables
Design: Copper conductors for power + fiber optics for data, with integrated shielding to protect both media.
Use Case: Deployed in the Lockheed Martin F-35’s avionics to balance EMI resistance and high-speed data needs.
c. Active EMI Cancellation Systems
Innovation: Sensors detect incoming EMI and generate counteracting signals in real time.
Example: Experimental systems in NASA’s X-59 QueSST supersonic jet mitigate lightning-induced interference.
4. Testing and Certification Standards
Aviation cables must undergo rigorous EMI testing:
Radiated Susceptibility (RS) Tests: Expose cables to controlled EMI fields (up to 200 V/m) to simulate extreme conditions.
Conducted Emission (CE) Tests: Measure unwanted EMI generated by the cable itself.
Lightning Strike Simulation: Cables are subjected to 100 kA pulses to evaluate shielding integrity.
Case Study: A shielded cable for the Airbus A350 XWB survived a 200 kA lightning strike test, meeting EASA’s stringent safety criteria.
5. Challenges and Solutions
a. Weight vs. Shielding Efficiency
Challenge: Heavy metal shields conflict with fuel efficiency goals.
Solution: Use lightweight materials like aluminum-coated magnesium alloys or graphene-enhanced foils.
b. Flexibility and Durability
Challenge: Repeated bending (e.g., in wing control surfaces) can crack traditional shields.
Solution: Corning’s OPTISHIELD™ cables incorporate flexible metallic meshes with self-healing polymer coatings.
c. Cost of Advanced Materials
Challenge: CNT-based shields are expensive to produce.
Solution: Scale production through partnerships, such as Boeing’s collaboration with NanoSonic on conductive nanocomposites.
6. Future Trends in Aviation Cable Shielding
a. Smart Shielding Systems
Self-Monitoring Cables: Embed sensors to detect shield damage or EMI breaches and alert maintenance crews.
b. Metamaterial-Based Shields
Innovation: Engineered materials that deflect or absorb EMI at the molecular level, offering ultra-thin, high-efficiency protection.
c. Integration with Electric Aircraft
Focus: Next-gen electric propulsion systems (e.g., in Eviation Alice) require shielding for high-voltage cables to prevent arc faults.